“There is nothing like a crisis to sharpen decision making.” — Supply Chain Leader Mirko Gojic
We all know that the past few years have transformed the supply chain function. The pandemic and other acute disruptions have placed—and continue to place—tremendous strains on global supply chains. It’s led to supply chain transformations across industries as companies seek to become more resilient and agile. Call it a supply chain evolution.
As a recruitment agency specialized in supply chain management, we love to interview senior leaders who are on the forefront of that evolution. People with a holistic vision for not only how the supply chain field has evolved, but how it will evolve into the future.

Mirko Gojic is just such a leader. He possesses an accomplished background in the Consumer Packaged Goods/Food industry, beginning in the supply and demand planning area, and growing his career to senior leadership roles encompassing a variety of supply chain disciplines including inventory, S&OP, procurement, and process improvement. During the pandemic, Mirko was a Senior Supply Chain Manager at a major consumer packaged goods company, tasked with delivering excellence in an environment changing at lightning speed.
Mirko learned a lot about how to make supply chains more adaptive, agile and collaborative. It turns out that many of these best practices aren’t just useful when responding to challenges—they’re actually the key to unlocking strategic value in the future.
So we were thrilled when Mirko agreed to an interview about his experience, and his thoughts about the field going forward.
We spoke about:
- The way that the supply chain function has transformed over the past 2+ years
- Major lessons learned from the pandemic, and how those lessons can drive sustainable growth and strategic competitiveness going forward
- Mirko’s advice for supply chain professionals looking to grow their careers
- And more.
Read on to check out our Q&A. We hope you’ll find it as insightful as we did!
1. Everyone knows that the past two and a half years have placed unprecedented pressure on supply chains, and organizations everywhere have had to adapt. Now that it appears that the most acute phase of the pandemic is passing, what are your thoughts on the state of the supply chain function after such a transformative period?
I believe the supply chain function broadly is the strongest it has ever been. There has been a massive focus on and general improvement in the understanding of modern global supply chains, within the general public’s eyes, but also internally to companies and governments. Worldwide Google search volume trends for “supply chain” tripled pre-and-post pandemic, which is a small anecdote that shows how supply chains have entered the public consciousness.
This general elevation of supply chain understanding and interest, and the massive disruption the pandemic has caused, means companies need to both be seen to be addressing the possibility of another massive global disruption, as well as actually making changes for improved resiliency to ensure they deliver their strategic goals. This work is not limited to one link in the chain. It will require broad risk assessment.
Hence, on top of day to day work, we have an accelerated drive for innovation to adapt to emerging trends, such as digital analytics for more effective and efficient analysis, and network development in support of eCommerce, which made major gains during the pandemic. Trends that existed before the pandemic became more relevant throughout the pandemic. As much as supply continuity was an important factor in supply chain design and review, the pandemic upended our entire perspective of what resiliency means.
So, there is no lack of work in the supply chain arena these days.
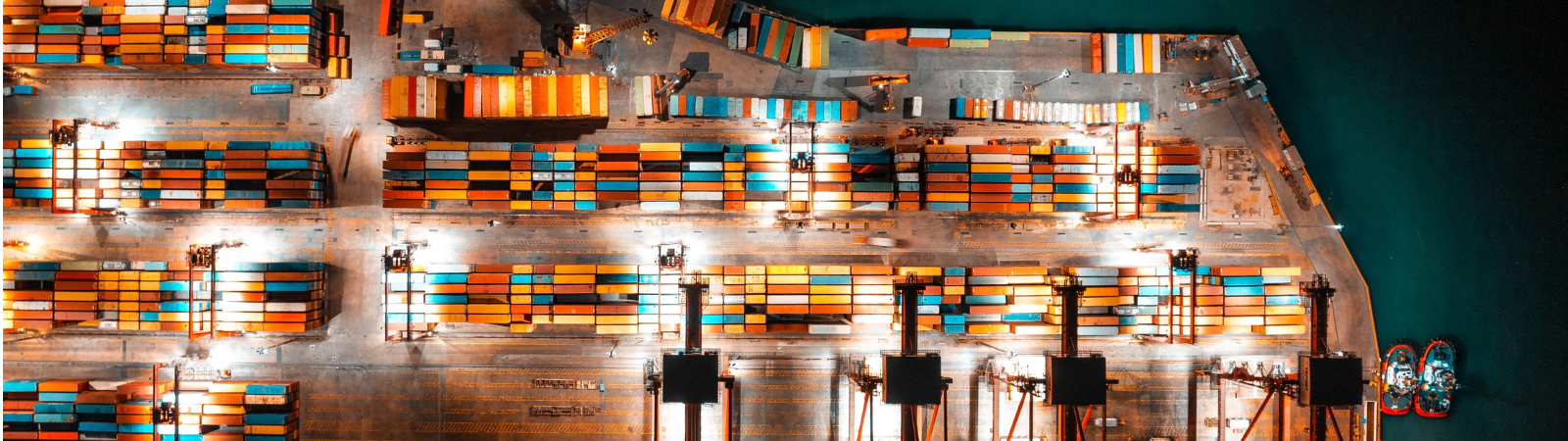
2. After two and a half years of working as a supply chain leader dealing with these disruptions, what are the biggest lessons? How can supply chain organizations manage this unpredictability?
In my experience, I would flag three big internal lessons from a supply chain planning and execution perspective, which is my focus area. (1) Simplicity is your friend, (2) collaboration massively increases during a crisis, and (3) supply chains have been finely tuned for optimization with limited excess or flexible capacity.
We saw forced simplification in the market by many companies, such as Coca Cola cutting a number of smaller brands, and Ragu sauce being pulled out of Canada. Concentration of effort focused their portfolios and doubled down on core business. These actions can drive long term benefits like reduced working capital, less changeovers in manufacturing, and done well, improved margins by targeting less profitable items. Companies who simplified their businesses thrived.
If we look at collaboration, the steady monthly review of business performance in a traditional S&OP process was not enough. Those lacking a developed S&OE infrastructure struggled with the speed and focus shift to short term execution, or hijacked their long-term focused S&OP. The lesson there is touild a robust short-term S&OE process to enable both.
Driving simplicity and building strong short-term market sensing mechanisms improve the ability to catch a trend and adjust enterprise approach, but one also needs reactive capacity. In some cases this will be solved through the influx of equipment such as rail cars, truck chassis, and ocean containers, but new multi-million dollar manufacturing sites can not be built to sit idle. Approaches like postponement and multi-sourcing reduce the pressure to build inventory bubbles or commit to massive capital expenditure.
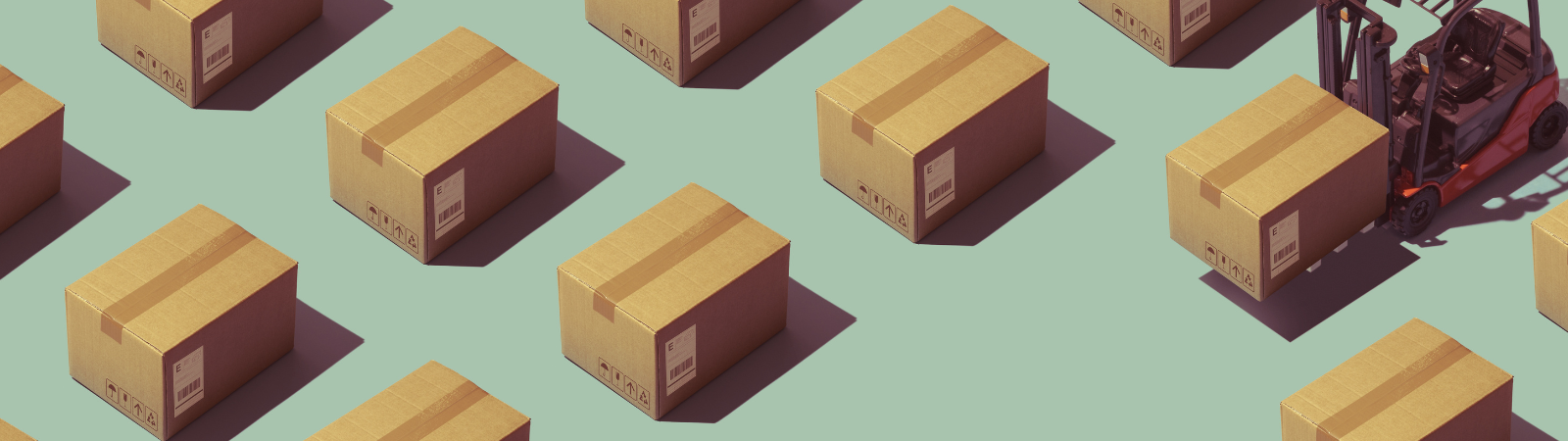
3. We’re interested in what has been learned, but even more interested in how to move forward. Is it fair to say that many of the changes organizations made during this period are best practices that will be even more useful in the future, or that should have been made anyway? As we think about the next 5 years of supply chain management’s development (especially in food/consumer packaged goods), what are some of the major trends that you anticipate? These can be technological, process-oriented, people-oriented or all three.
Absolutely. Many of the changes made during the pandemic were already part of ongoing business management, but there is nothing like a crisis to sharpen decision making. The pandemic pushed us to make harder decisions. Maximizing portfolio focus leaves lasting benefits in business shape and organizational focus, postponement drives tremendous value in working capital (inventory) and ability to service short-term market shifts, and well developed and differentiated processes which drive strategic intent through operational execution are best practices.
Some of the above will appear to obstruct growth objectives. This is why the decisions can not be made in a silo, but we now have more time to collectively evaluate the right actions to best deliver strategic business objectives.
Hence, looking forward I believe the intense focus on supply chain development will continue. Investments in digital enablers for more efficient and effective translation of insight to action, the development of enhanced short & long term collaboration, and network review and re-design must adapt to the new normal in trends like eCommerce and greater global instability.
All of the above means a greater need for talent in supply chain. It takes time to develop robust leaders and functional experts who can drive these initiatives. The good news is the graduating class of the COVID-19 cohort had a front row seat, albeit an uncomfortable one, to see how changes impacted business shape and how critical supply chain functions enable strategic execution.
4. You’ve had a major role in developing S&OP and other processes, as well as implementing and operationalizing systems improvements. What would your advice be to companies who feel that their systems and processes aren’t giving them the supply chain agility, and visibility, that they need? What’s your strategy for making these big-pictures changes, and getting all the boats rowing in the same direction?
My advice is to leverage the learnings we’ve discussed while they are still fresh in mind. Use the three internal focus areas to build capability and resiliency in your supply chain.
Plan to invest for some time in both staff and technology. Remember that change takes time and can be hard on people. Hire and develop those who understand the critical nature of supply chain functions to long term business strategy and short term operational execution.

5. As a recruitment agency focused on supply chain, we’re always interested in questions around talent in the field. As a supply chain leader, you’ve had a deep insight into what makes teams perform at a high level. As we move to a “Post-pandemic” environment or something like it, have the key skills for supply chain professionals changed? What would your advice be to someone who’s working as, say, a supply chain planner and looking to grow their career towards becoming a manager or senior manager some day?
I don’t think the fundamentals have changed much. If you are starting fresh, begin with a functional area and develop expertise. Own your career development. Seek opportunities to expand your knowledge base and be clear with your manager about your career objectives so that they can help open doors by exposing you to experiences and skills that you will need. Be patient.
Develop an absolute love and passion for data, analytics, and storytelling. For example, a clear advantage today is familiarity with some of the great visualization tools like PowerBI or Tableau. Visuals are a key component of storytelling—the art of capturing an audience and delivering a call to action. Excel is not good enough anymore.
Seek to understand how your work impacts the bottom line and help those around you to understand their importance to drive engagement.
Finally, in supply chain, you connect and exert influence with so many functions and people, often with competing interests or agendas. Treat everyone with respect and seek to understand their position so that you can effectively overcome barriers. Leave anyone you touch with a sense of value so that you can have positive long-term relationships.
If you drive massive value, help those around you deliver massive value, and develop yourself as a sought after collaborator you will do very well.
A big thanks to Mirko Gojic for taking the time to do this interview. We hope you found it as full of insights as we did. Head to Mirko’s LinkedIn page to learn more about his background in supply chain—and if you’d like to get in touch with him, we’d be happy to arrange a connection! Please email recruit@argentus.com.
And stay tuned in the future for more interviews with leaders from across the supply chain industry about some of the biggest issues facing the field today.
0 Comments