An explainer from Canada’s leading recruiters in the field.
On the Argentus blog, we often get deep into the nitty gritty of various aspects of supply chain management from a talent perspective. As recruiters specialized in the field, we love getting into the weeds. Whether that means giving detailed career advice to candidates looking for jobs, or providing business intelligence to companies looking to hire in supply chain. We hope our blog is a useful resource for anyone in the industry to understand the hiring landscape: what skills are companies looking for when they’re hiring? What are the biggest barriers companies have to filling their jobs? These are the questions we seek to answer.
In this effort, sometimes it helps to get back to brass tacks. Terminology in supply chain management can be confusing—mostly because different companies use it differently. Sometimes we write posts that aim to clarify this confusion. Often, these distinctions have big implications for how companies hire in the field.
A few weeks ago, we posted our explainer about the differences between Supply Chain Management and Procurement. We were thrilled by the amount of attention and commentary it received.
So today, we want to write another post along the same lines. In this case, we want answer the question:
What’s the difference between Supply Chain Management and Logistics?
This is a big one.
“Supply Chain Management” and “Logistics” are often used interchangeably—less so than they used to be—but they have some key differences.
What’s more, these differences are actually a great entry point into understanding the key strategic contributions that Supply Chain Management makes in a variety of different industries. How a company uses the terms “Logistics” and “Supply Chain Management” can tell you a lot about how that company operates, and their level of strategic sophistication.
(Please note: when we’re speaking about “Logistics” we mean in the business sense. There are many other things in the world that require Logistics outside of moving physical goods, but we’re only concerned with corporate Logistics for the purposes of this article).
In short, Logistics is a discipline within the larger function of Supply Chain Management. This holds true pretty well across almost every industry. But there’s more to it than that.
Here are our basic definitions of each:
- Logistics is the movement of physical goods, either raw materials or finished goods, between suppliers, factories, warehouses, and consumers. This includes trucking, shipping, air freight, and/or rail freight. It’s an important tactical part of getting a product, or products, to market.
- Supply Chain Management is also concerned with the physical movement of goods. But it refers to the broader function of everything involved in getting products to customers—not just the actual movement. Who are you buying the product from? For what cost? Why? How is the product being manufactured? How much of this product do we expect to sell, and how much should we hold as inventory to meet these needs? What big disruptions can we expect to our supply, and how do we manage that risk? Supply chain management aims to answer all these questions and more. And for that reason, it’s a key strategic function for companies.
The tactics vs. Strategy piece is important. In general, Logistics is a tactical part of supply chain strategy. Logistics can be strategic in and of itself, but it’s only one piece of the bigger picture.
To really dig into the difference, it helps to get into the history of each term.
Digging into Logistics:
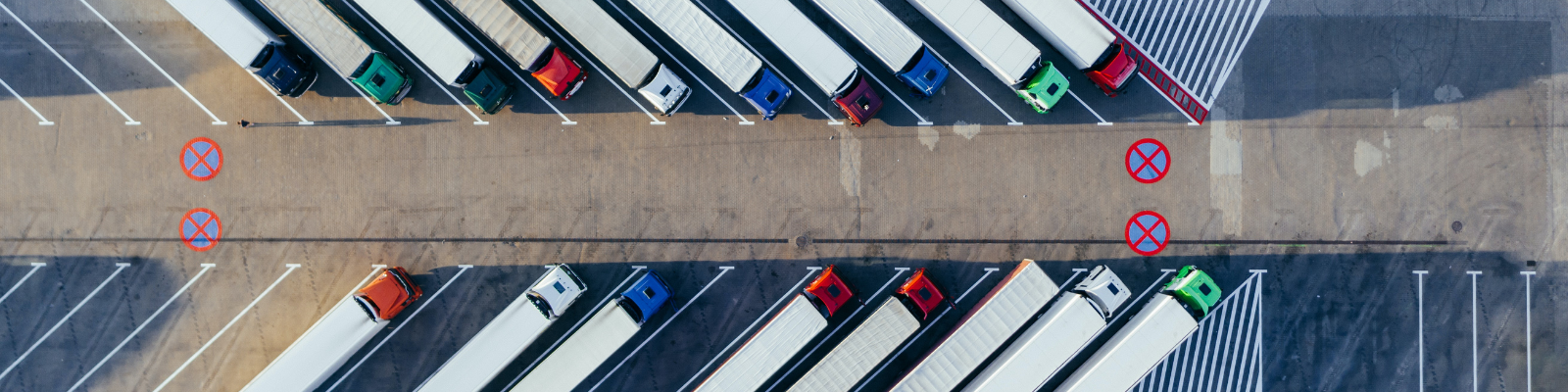
As a discipline, logistics has its roots in military history. Military leaders as far back as the Roman era became concerned, in a systematic way, with the most efficient way to feed, clothe, house and supply their military forces. Later, in the 19th century, the term “Logistics” (from the French logistique, from “loger,” the verb “to lodge”) arose to describe supply of increasingly complex, mechanized militaries as they waged wars across Europe. As the industrial era continued, Logistics became more and more important to military affairs, to the point where it became a key determining factor in several major conflicts.
During the first half of the 20th century, Logistics evolved to encompass the movement of goods outside military contexts as well. Corporations, governments, non-profits, and many other kinds of organizations hired logisticians to manage the physical flow of goods.
Today, Logistics is a crucial tactical function for any company that brings physical products to the marketplace. It includes the management of the services that move those goods from factories, to warehouses, to the consumer. The main modes of logistics today include air freight, rail freight, trucking (land freight), and ocean freight. Logistics professionals also manage the process and documentation around import and export of goods, including trade requirements, customs, duties, and other considerations. Some people consider Warehousing to be a logistics function, while others consider it to be part of the larger function of Supply Chain Management.
Typically, companies either manage their Logistics in-house, or use “3rd party logistics” (3PL) firms. These providers typically have their own transportation fleets and competencies to manage the process. Using a 3PL allows companies to outsource logistics as an aspect of their overall supply chain management—which can bring huge efficiencies to the way they move goods.
It’s also worth noting that many companies separate “Logistics” and “Distribution” into two separate disciplines. For these organizations “Logistics” refers to the movement of goods from suppliers to factories and warehouses (for example, shipping raw materials from overseas), and “Distribution” refers to the process of getting products from those warehouses to consumers. That being said, many companies put this all under the Logistics umbrella, including the all-important “Last Mile Logistics” of delivering products directly to a consumer’s door.
Digging into Supply Chain:
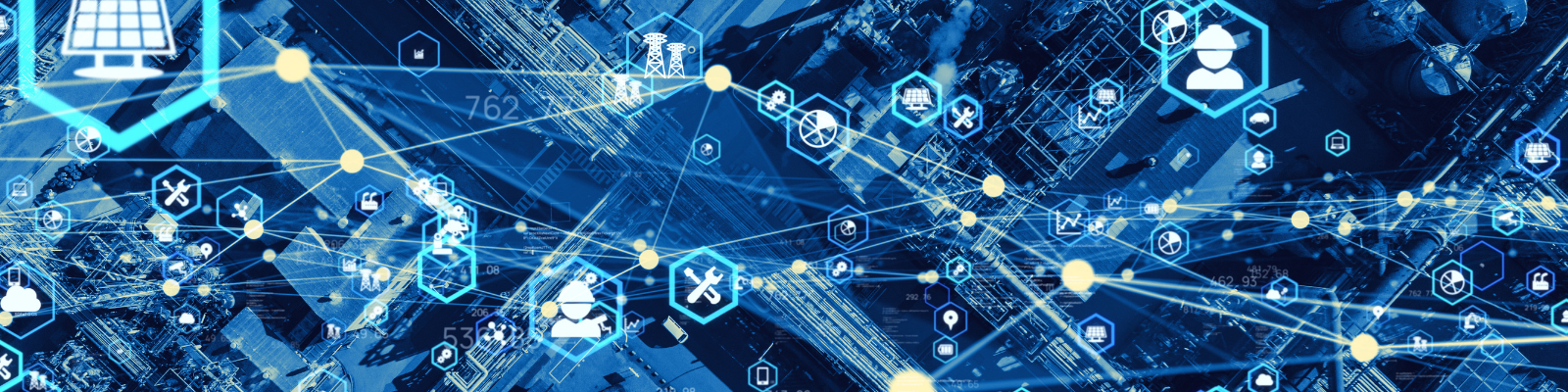
As a discipline, supply chain management grew out of logistics. In the 1980’s, a consultant at Booz Allen Hamilton named Keith Oliver first introduced the term “Supply Chain Management” as a way of describing the overall optimization of the flow of goods from product to consumer.
There are several organizational and technological changes that allowed Supply Chain Management to develop as a distinct strategic function. For one, companies recognized that there’s more to product flow than just having the adequate supply—and a more holistic vision of how products come to market could pay huge dividends.
For example, Lean Manufacturing grew out of Toyota’s management culture, which placed an emphasis on continuous improvement in the manufacturing process, and “just in time” inventory practices arose. Instead of stockpiling inventory, by having “just enough” inventory necessary for production (in manufacturing), or to meet demand (in manufacturing and other industries), companies could save money and reinvest it in new products, marketing, capital expansion, or other growth. In recent years, companies have redefined their inventory strategies to make them more resilient in the face of disruption. These strategies may shift with time—but that shift, and the process of being strategic about these individual elements, is the essence of supply chain management.
Alongside organizational improvements, technologies such as Enterprise Resource Planning (ERP), Materials Management (MM), Transportation Management (TMS), Warehouse Management (WMS) and other systems allowed organizations to capture and manage data, and uncover supply chain efficiencies in a way that was never possible before.
Since the ’80s, these two trends have led to a flourishing of sub-disciplines in Supply Chain that aim to improve efficiency, and extract value from every part of the process. For example, Demand Planning seeks to predict demand for products using trends and forecasting, aiming to hit the sweet spot by producing just enough to cover that demand. Strategic Procurement looks to broaden and improve the supplier base, attaining cost savings while also adding value through sustainable procurement, or by adding more diverse suppliers.
These functions are all various “silos” contributing to the overall picture of supply chain management. The top organizations are able to closely integrate these functions, using technology and process to get their teams on the same page. They can match the supply chain strategy to the overall strategic goal of the company. They can build a pipeline of new technologies to improve that capability, and align the supply chain with basically every aspect of a company’s business. Then, when conditions on the ground change, or when company strategy changes, they’ve built a responsive supply chain that can pivot.
It’s no small task.
Implications for hiring:

Of course, this is how we see it. Supply Chain Professionals and Logisticians may disagree. There are people who have “Logistics” titles who do more than just Logistics. And there are people with “Supply Chain Manager” titles who only do Logistics. Which, of course, is fine.
But the way we use these terms has implications for people looking for jobs, companies looking to hire, and people looking to expand their skills. It’s not just a semantic difference.
For example: if you’re getting into the field, the sooner you understand the difference, the better. It helps to evaluate educational opportunities, as well as entry-level roles. Are you someone who wants to solve problems and provide an exceptional experience for customers? Maybe logistics is a good discipline to learn. Do you want to use data and a variety of integrated approaches to examine all aspects of supply, and help develop strategy? In that case, aim for supply chain. In either case, recognizing that logistics is a subdiscipline of supply chain management is a useful bit of knowledge.
If you’re a company looking to hire, and build your business, you might understand this distinction and have a set strategy in place for each. But it’s possible that you don’t. If your company is small, logistics seems sufficient. You can evaluate 3rd Party Logistics and Fulfilment providers and outsource the process. But it’s important to recognize that if your company grows, it’s worthwhile to invest in broader supply chain capabilities. It’s easier to add them now, and scale them later, than implement them after growth.
For hiring, it’s important that companies recognize the transferrable skills between the two, but also to make the distinction to attract the right candidate pool.
To help drive home the point, here’s our list of the core competencies for Logistics and Supply Chain Management. Hopefully it will help clarify the overlap, as well as the differences between the two:
Core disciplines for Logistics include: Ocean freight management, road freight management, air freight management, rail freight management, transportation management, customs, freight forwarding, shipping, distribution, warehousing (by some definitions), reverse logistics (managing product returns), couriers, last mile logistics (the service that hands a delivery to a customer).
Core disciplines for Supply Chain Management include: logistics, purchasing (raw materials and finished goods), indirect Procurement (goods not for resale and corporate services), transportation, warehousing, customs, shipping, supply planning, inventory planning, demand planning, sales and operations planning, network design, manufacturing, production scheduling, production planning, continuous improvement (e.g. Lean Six sigma), and others. It also includes the implementation and management of systems related to digitally managing these functions (e.g. Enterprise Resource Planning, Materials Management, Manufacturing Resource Planning, Warehouse Management Systems, Transportation Management Systems).
We hope you found this guide useful! Do you have anything to add, or disagree with our definitions? Let us know in the comments! And if you have any questions about the differences between Supply Chain and Logistics, either in your own hiring, or as you seek to develop your career, reach out to Argentus!
0 Comments